Floor Facts
We’re here to help you understand the nature of concrete and why it’s so hard to keep coatings, paint, and floor coverings on it. Explore this page to find answers to many common concrete issues. We hope that, armed with this information, you can avoid the expanse and hassle of redoing your concrete floors.
Explore specific topics by clicking below.
Cement gel is a jelly like swelling that occurs around each grain of Portland cement when water is added to the concrete mix. Aggregate gel is essentially the same. It is the initial reaction product between cement and water. The gel is the controlling factor in cracking, uniformity, and structural quality of concrete. Cement gel relates to the size of the voids and pores in concrete. The cement gel imparts fatty and cohesive properties to the mix. As hydration of the cement proceeds, the gel partly crystallizes and on drying, reverts to almost the original cement grain size. Gel size and hydration can vary widely, depending upon water available and temperature. It is these variations throughout the concrete which causes variations in the quality and porosity of concrete for a given mix design. In the heat of summer, gels form faster and longer, and large gels absorb more water from the mix.
Thus, the resulting concrete has poorer quality. As water is consumed by hydration and rapidly lost through evaporation, internal stresses are created. The eventual results are shrinkage cracks. In cooler weather, gel formation is retarded. Smaller gels are formed, take longer to form, consume less water, and as a result less water is required. Because hydration is slower, less shrinkage occurs, concrete is more dense, and usually has a higher structural quality.
One area of controversy today is how to properly cure concrete. In the interest of speed and increasing profits, the use of “curing agents” which are sprayed over the concrete to retard premature drying has become the norm.
However, in my opinion, there is no substitute for the old “water cure” for concrete…where the slab is kept wet for 5-7 days after finishing, by flooding with water or using burlap etc to cover the slab and keep water on it. The strength and density of concrete cured by this method will always be exceedingly better than concrete which is just finished, sprayed with curing agent and left to dry.
So if you ever pour a new slab of concrete, make sure you insist on water curing. Concrete that is water cured for 7 days can show as much as 50% greater strength and be much more dense.
My Solution: Concrete Remedy DS, due to its chemical reaction forming a silica aero gel, aids in retaining the water in the concrete during the hydration/curing process, resulting in a higher quality concrete. For this specific application, using Concrete Remedy DS as a cure for new concrete, a coverage rate of approximately of 150 – 200 square feet per gallon is recommended.
Capillarity is the transmission of moisture and water in masonry. By definition, it is the action by which the surface of a liquid, where it is in contact with a solid, is elevated or depressed. The elevation or depression is caused by capillary action. By capillary action, moisture may travel from a lower to higher elevation or can travel in any direction. The amount of moisture that can be transmitted from the ground by capillary action is often underestimated, if understood at all.
Tests by the Housing and Home Finance Agency (US Government) conducted at the Forest Products Laboratory have clearly indicated that as much as 12 gallons of water per 1,000 sq. ft. per day can be transmitted through a concrete slab and, if permitted, evaporates into the air.
When the slab is covered by floor covering, this moisture will carry alkalis, salts or additives from the concrete. This will collect under the floor covering and attack the bond of the adhesive, resulting in destruction or deterioration of the adhesive itself.
This same principal also applies to vertical concrete, where fog, dew and dampness can collect causing paint and other sealants to peel or wear off prematurely. The distance which water will rise from the ground by capillary action is also underestimated. Test by the same US authority indicate that moisture can climb form a water table that may be 20 feet below the ground or slab.
Obviously, general ground dampness speeds up the transmission of moisture. It is suspected that this transmission may result from a combination of capillary, absorption and various pressures rather than capillary alone. Nevertheless, moisture can migrate from this depth.
My Solution: Concrete Remedy DS, due to its unique penetration factor and chemical reaction with alkali its ability to fill voids and create a solid mass, and its ability to hold a hydrostatic head, will eliminate the problems associated with capillary action.
A simple test can establish the amount of Concrete Remedy DS required to solve the problem. After your first application, merely tape down several pieces of ordinary dry sponge or foam rubber to the treated surface. After 24 hours, under normal conditions, the sponge will appear dry and the job is completed. However, in extreme problem areas of excessive moisture and seepage, the sponge will be be damp to wet.
When this occurs it is an indication the treatment must be repeated as many times as is necessary until the sponge is dry after 24 hours. The Concrete Remedy DS treatment is now permanent. No other waterproofing treatment will EVER be necessary.
Alkali is never pure and rarely stable. It is made up of combination of elements and almost always reacts with other elements or chemicals. We start with hydrogen; then lithium, sodium, potassium, rubidium, cesium and francium. Francium is radioactive with a half-life of 20 minutes. The other five are the very active alkali metals. Each element has electrons and molecules which are always eager to take part in chemical reactions with other elements. The two most important alkali metals are sodium and potassium. We find a hint of them in potassium carbonate and sodium carbonate. Sodium makes up 2.6% of the earths crust and potassium makes 2.5%, yet we never see them. They are always found in combinations with other elements. Neither of them could remain in a pure state in air or moisture.
The increased use of concrete subfloors in direct contact with the ground makes it more important than ever to completely understand the moisture and alkali inherent in these subfloors and their effects on paints and floor coverings.
Well known as the “alkali problem”, this condition is primarily a problem of moisture.
Alkali is present in every concrete slab and is more detrimental when moisture is present.
On adequately ventilated suspended concrete subfloors, moisture is not present in troublesome quantities. However, when the slab is in direct contact with the ground or a poorly ventilated air space, moisture is brought up through the slab by capillary action. It dissolves the alkaline salts in the concrete and appears at the surface as a destructive alkaline solution causing spalling and efflorescence.
Although moisture and alkali conditions can vary greatly, there is always sufficient moisture in the ground and alkali in concrete to present an alkali problem on subfloors.
It is never safe to assume that a concrete slab will always be dry because it has been dry until now.
When paint or floor coverings are applied, even a small undetected amount of moisture can cause coverings to warp, buckle or separate from the concrete surface.
My Solution: Concrete Remedy DS will alleviate this problem by sealing, waterproofing and moisture proofing the concrete slab eliminating spalling and efflorescence, leaving clean surfaces similar to ” etching ” to which paint or mastics and adhesive can effectively secure a better bond with. Concrete Remedy DS treatment will eliminate these destructive, moisture and alkali related problems for ever.
The following is a quotation from Chemistry and Technology of Paints, by Maximilian Toch, published by D. Van Nostrand Co., New York, New York: ” Portland cement is a rocklike alkaline lime substance composed of sand and / or gravel mixed with cement and water.
In attempting to apply paints, adhesives or floor coverings, it is recommended to clean the surface first. Surfaces are cleansed with muriatic, sulfuric or acetic acids. The application of these acids to Portland cement destroys the cement because they dissolve out the lime and leave the sand and aggregate loosely bound. Portland cement floors ‘ dust up’ merely under the abrasion of (shoe) heels. Factories that have machinery, calculators, electronic or delicate instruments have found it impossible to operate under these dusting conditions. To alleviate these conditions, paint or floor coverings are used.”
The above quotation is used to illustrate that concrete alone, by its very nature, creates a multitude of problems.
Coatings such as paint and floor coverings are used in an attempt to alleviate or enhance the use of masonry.
However, such coatings have proven completely ineffectual when excessive moisture and alkali contents are present.
Concrete dusting, ( small particles of the surface broken free) , is caused by any vehicular, foot, machinery and other traffic over the concrete surface. Dusting is a costly foe to efficiency due to damages it causes to machinery, merchandise, other equipment, and environmental health. In extreme situations dusting can be classed as wear due to abrasion (i.e. high traffic areas like bridge decks, garages, stairs, etc.) and the result can be costly premature replacement of the surface or structure.
My Solution: Concrete Remedy DS’s chemical reaction with the alkali and lime which causes the independent particles of concrete to solidify, harden and strengthen the concrete, along with its ability to stop the penetration or transmission of moisture, can permanently eliminate dusting and abrasion due to wear for Ever.
Concrete Remedy DS can eliminate the necessity of a floor covering.
Floor covering failures are often caused by one or more combinations of the following: Moisture, Alkali, Hydrostatic Pressure, or Differential Humidity between the slab and the interior of a building.
It should be noted that the main cause of floor covering or coating failure, including paints, is not the fault of the product. Instead, improper preparation of the concrete can account for nearly 80% of all failures.
If you fail to control the moisture/alkali problem within concrete, you have failed to properly prepare the concrete. Simply covering the concrete with a surface coating to serve as a moisture barrier will not solve the problem because the problem originates down in the concrete. As that problem develops, it will cause the moisture barrier to lose its bond with the concrete, and then the coating or floor covering will fail as well.
To apply asphalt, vinyl or rubber tiles and other floor coverings, there usually must be some site preparation consisting of the removal of contaminates and loose particulate/dust from the surface to be covered. Mastics or adhesives of some kind must usually be applied in order to bond the covering to the surface. We are aware of the make-up of concrete and the problems built into using it in the form of alkali, lime and moisture. We are also aware of the factors of porosity and how the water used to mix the cement and aggregates evaporates during the long curing period leaving mass voids and pores through which moisture passes and mixes with the alkali.
When the slab is covered, the drawing action (from capillary action) on the moisture in and under the slab, is greatly increased. When this alkali-rich moisture is drawn up into contact with the adhesives, the following occurs: The adhesive emulsifies or starts to deteriorate, resulting in bubbles or blistering which cause warping, cracking, and peeling (off) of the adhesive and/or the cover, necessitating replacement of one or both, at substantial cost.
My Solution: Concrete Remedy DS, due to its internal chemical reaction caused gels, its ability to hold a hydrostatic head, and the fact that it is not a surface, but, an internal sealer, will solve the problems related to the floor covering trade because Concrete Remedy DS prevents the moisture from reacting to alkali and then being drawn up into contact with the adhesives or mastics for EVER.
It has been noted that the pH of moisture under failed coatings and floor coverings can be as high as 13 – a condition that the best adhesives or paint cannot withstand.
Please Note: It must not be overlooked by applicators that Concrete Remedy DS is an internal sealer, and as such, the surface to be treated cannot absorb the product well unless it is bare.
The surface must be free of any surface coating or contaminant prior to the application of Concrete Remedy DS.
Why do paints blister or crack on concrete surfaces?
It is due to a problem called saponification (soap creation). When soap is manufactured, the basic ingredients are a form of alkali and oil. The combination of alkali in the concrete and the oil in the paint causes saponification, which in this case is more commonly identified as flaking, blistering, and peeling of paint from the surface. Even the much improved vinyl, rubber and latex based paints tend to peel and crack off of the surface.
The prime reason for this is that the alkali and lime are still “fighting” the paints. If these coatings are being used to seal or waterproof the surface they will need to be reapplied periodically to be effective, requiring costly stripping before each re-application, or the formation of many layers of material in various states of decomposition. Such multiple layers will not allow the concrete floor to breathe, and if concrete can not breathe it will decompose and disintegrate.
My Solution: The application of Concrete Remedy DS to concrete surfaces will give a permanently alkali and moisture free surface for better bonding of paints. When applied in accordance with the manufacturer’s directions, the paint life on a structure can be increased up to 300%, providing a longer ‘ fresh paint ‘ appearance and reducing maintenance cost.
Concrete Remedy DS treatment is essential if concrete is to be painted.
Close examination of the concrete, after Concrete Remedy DS has been applied and the surface washed, will reveal clean pores. In many cases this has the same effect as ‘ etching’ which is quite often necessary prior to applications of paints and adhesives for better bonding.
Any surface treatment or coating must be removed prior to applying Concrete Remedy DS to allow it to penetrate the surface. On occasion, foreign matter such as grease and oils will be floated to the surface by the Concrete Remedy DS as it penetrates the concrete. This foreign matter should be flushed off with water prior to painting. In areas where there is an excessive amount of foreign matter, several rinses may be necessary.
With respect to wall sweating, it should be remembered that the surface of most common concrete building materials have an affinity for water molecules. This molecular film is proportionate to the relative humidity. At saturation points, all voids, pores and capillaries can become completely filled. When the atmospheric conditions, inside or outside, (which caused the excessive moisture in the first place) is alleviated, the porous wall may become filled to saturation point with moisture in liquid form. This condition then provides an excellent opportunity for (water) vapor to travel within a wall or structure.
In its travels, the vapor may strike a cold(er) area or dew point and condense in sufficient quantities to reach the interior wall surfaces and appear as wall sweat or bleeding. Both sweating and the condensation which causes it, can be greatly affected by temperature, humidity, wind velocity, soil moisture conditions, etc.
These conditions, if allowed to go unchecked, can cause peeling paints, spalling, formation of mildew, and efflorescence resulting in heavy maintenance costs. All porous masonry materials will be subject to the same conditions unless the proper steps are taken to avoid such conditions.
My Solution: The application of Concrete Remedy DS in the same manner as for waterproofing, will, due to its unique capabilities and results, stop these conditions which lead to wall sweating, FOREVER.
Did you know that the concrete floors of your dogs’ kennels are a perfect breeding ground for bacteria, mold and mildew? Concrete is a porous material and acts similarly to a sponge. When liquids are spilled on it, they will soak deep into the concrete. These damp pores in the concrete provide the perfect breeding ground for bacteria, mold and mildew.
Dampness is the critical element in bacteria, mold and mildew and pathogens multiplying. By stopping perpetual dampness, you remove that critical element.
Beyond the question of liquids with contaminants soaking down into concrete from above, there is the issue of the WICKING nature of concrete.
A 1000 square foot slab of concrete is capable of “wicking” 12 gallons of moisture per day, from as far as 20 feet below the surface. That is significant moisture.
My Solution: The Concrete Remedy Kennel Solution eliminates the breeding ground for bacteria in your kennel floor by preventing moisture from getting into your concrete. Both from ABOVE and from WICKING up from BEKOW. It will make your kennel safer for your dogs, easier to clean and reduce urine odors by preventing the urine from penetrating into the concrete.
Maybe you’ve never tried it. I mean lying on concrete. But your dogs may spend hours doing just that. Even concrete that doesn’t look wet is generally damp.
Remember, concrete actually wicks moisture from as deep as 20′ below the surface. What this means is that there is almost always moisture IN concrete. If it rains, or after you clean your kennels, the moisture is IN the concrete long after the surface dries. Even if you have applied a topical sealer or paint, there still will be moisture down IN the concrete.
Lying on continual dampness and cold can aggravate or contribute to aches and pains. When concrete is damp – even though it looks dry on the surface – it doesn’t warm up under your dog. Your dogs will be much more comfortable and avoid the dangers from damp concrete if their body heat warms up the area they are lying on. Since most dogs can’t talk, we felt it was important to tell you this on their behalf.
My Solution: Applying Concrete Remedy Deep Seal (DS) and Concrete Remedy Top Seal (TS) stops concrete from soaking up moisture from the ground and prevents it from holding moisture internally. By fixing your concrete so no moisture gets into it, from above OR below, your dogs will be much more comfortable.
MYTH
Concrete is like a rock.
FACT
Concrete is not a rock. To the contrary, concrete is a living and changing chemical composition. It is filled with voids and canals and absorbs liquids, even wicking moisture up into it. It's more like a sponge. Concrete wicks moisture. A 1,000 square foot slab of concrete can wick 12 gallons of moisture PER DAY from as far as 20 feet below the surface!
MYTH
All concrete is the same.
FACT
Concrete is extremely variable. Even in the same slab, you will find variations and differences in appearance and quality. Many factors determine the quality of a concrete slab. Major issues are: the ingredients, e.g., proportion of water to cement, type of cement and the type and cleanliness of aggregates. The most critical issue for quality of concrete has to do with how it was finished and cured. Weather conditions have a huge role in determining the quality of concrete.
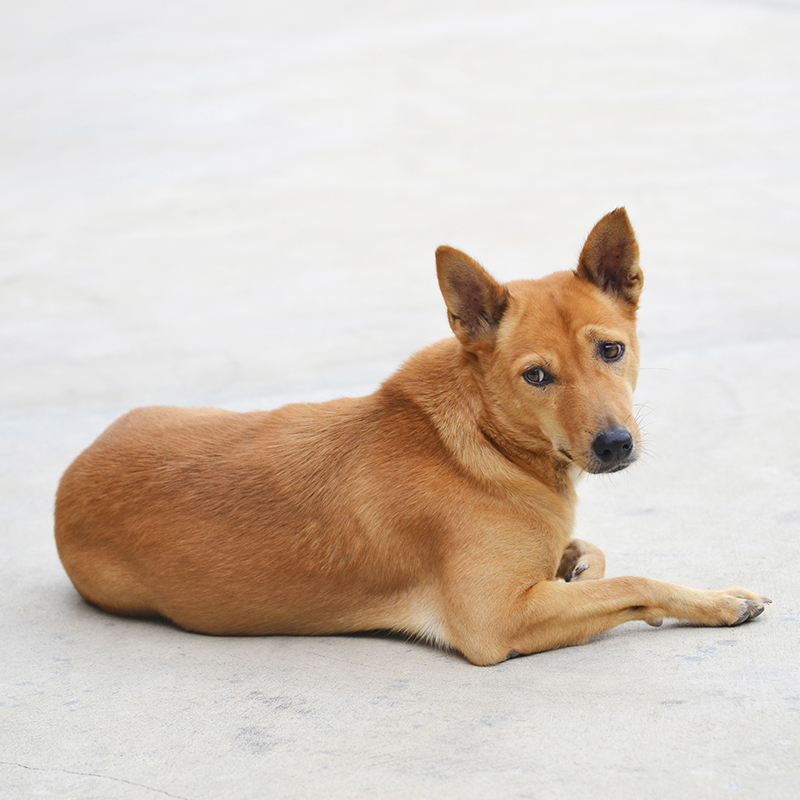